PRE - LEACH, VULCANIZING,
POST - LEACH
The gloves are pre-leached in 80 ft. length of treated hot water to wash off non-rubber particles and rubber chemical residues that could otherwise remain on the glove and cause allergic contact dermatitis. The water used in the leaching tanks is treated to prevent bacterial contamination and heated to improve leaching efficiency. The system includes four pre-leach tanks of hot flowing water, which are constantly monitored to meet required parameters.
The gloves are properly vulcanized to ensure the best physical properties and to reduce moisture content. They are then post-leached again in 60 ft. length of hot flowing water at 70-80°C. This process washes off much of the extractable water-soluble latex protein, residual chemicals, and other non-rubber particles. Extensive pre-leaching, post-leaching, and vulcanizing are some of the critical measures taken to offer you a safer glove.

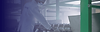
PROCESS
Crafting unmatched comfort and protection.
MANUFACTURING
The manufacturing environment and process have been designed to achieve the critical in-built quality necessary for a medical device, as per GMP requirements. The factory has a clean, hygienic, dust-free manufacturing environment. The plant is completely enclosed, and the factory has controlled exit and entry points with a positive air filtration system, following GMP guidelines for the manufacture of medical devices. This ensures that the gloves are uncontaminated with a low bio burden.

IN HOUSE COMPOUNDING
Carefully selected non-toxic rubber chemicals with safe levels of concentration are used in the process. The compounded latex is further clarified to remove any excess chemicals. All raw materials are quality-assurance inspected, and only materials of the highest standards are used.

POWDER FREE GLOVES
The Polymer Coated Powder Free Gloves are processed in a designated, specially maintained area. The extractable latex protein content of these gloves is less than 50 μg/dm2. We also manufacture a range of Powder Free Speciality Surgical Gloves.
QUALITY CONTROL
In addition to the standard airtight and watertight tests, each batch of gloves is electronically tested for micropores. Even though controlled production produces gloves with less than 1% pinholes, 100% inspection is carried out, involving over 250 skilled and trained personnel, to offer you a defect-free glove with a factory A.Q.L. of less than 0.65, as opposed to international norms of 1.5.
The well-equipped laboratory has all the facilities and equipment to test the quality of raw materials, physical properties of gloves, and protein content of gloves using a spectrophotometer. Estimation of protein is conducted for every batch of gloves, as per ASTM D-5712, using the Modified Lowry Method. The in-house microbiological laboratory also monitors bio-burden levels and sterility. The laboratory is equipped with a laminar airflow cabinet and is manned by trained and skilled microbiologists.


PACKAGING
A separate building is engaged for housing the packing section into which only quality control passed gloves are allowed to enter. The packing section is clean and dust-free with positive pressure filtered air system with controlled exit and entry points. It is kept clean and fumigated at regular intervals to ensure low bio-burden level. State-of-the-art packing machines are installed for walletting, pouching and sealing the gloves automatically thereby reducing human contact with the gloves to a minimum. The walletting Machine prints and folds the wallets in-house thereby reducing contamination. The pouching machine is specially designed for automatic packing of gloves. It incorporates skip sealing, photo electric cell for registration as well as a flexography system for printing of batch and other manufacturing details.
Moreover, the Pouching Machines ensure an aesthetic packing system and the integrity of the pouches. The entire process is done in a controlled and clean environment. The end result is very little chance of contamination and a great degree of hygiene. The packed gloves are once again quality assurance checked and passed for sterilization.


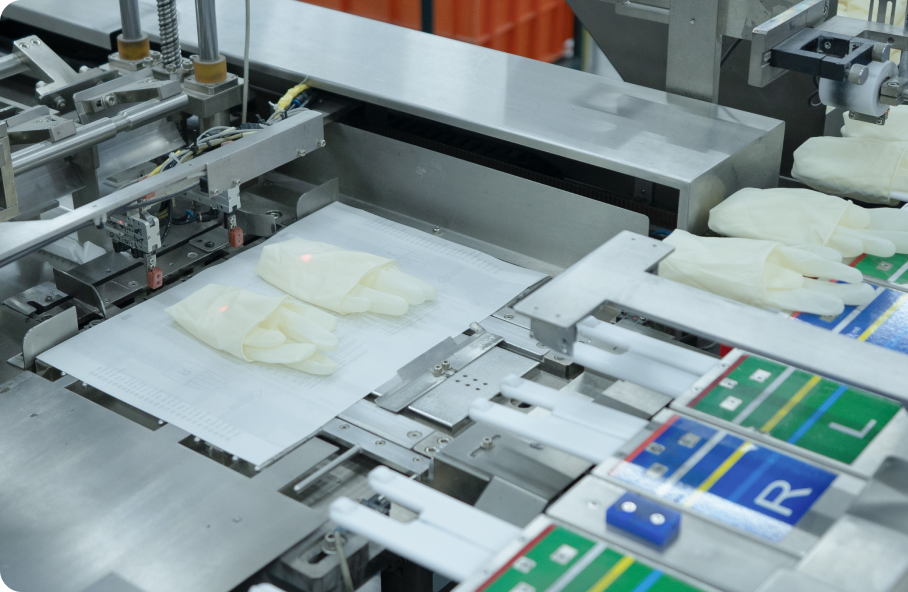
STERILIZATION
State-of-the-art P.L.C controlled E. T. O sterilization plants with a double door system are installed which is validated to ISO 11135 norms. Each process cycle’s efficiency is monitored with bio-monitors. The process cycle also includes sufficient air wash cycle to ensure that residual E. O. on the glove is low.
The carefully selected packing material used ensures that it is suitable to permit E. O. sterilization and maintain sterility during transit and storage for the shelf life of the product. The sterilized gloves are tested for sterility in the in-house Microbiological Laboratory. Kanam has started its own gamma sterilisation unit under the name Gamma Tech India Private Limited. Kanam now has access to ETO sterilization and gamma sterilisation in house.
CORRECTNESS IN PAIRING
CORRECTNESS OF MARKING ON POUCH/BOX
CORRECTNESS OF TYPE, SIZE AND QUALITY AS PER ORDER
CORRECTNESS OF PACKAGING MATERIALS
COMPLIANCE TO ALL PREVIOUS INSPECTIONS AND TEST REQUIREMENTS
CORRECTNESS OF STAMPING PARTICULARS
CONFORMANCE TO SPECIFICATIONS OF THE RELEVANT GRADE OF GLOVES
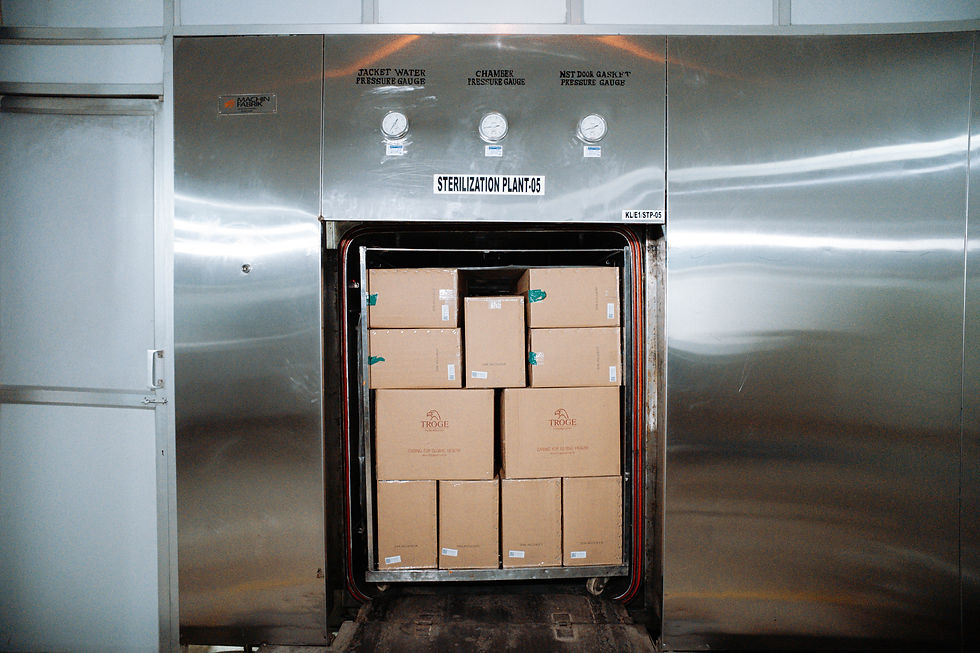
.png)
WAREHOUSING
We have a large warehouse with the capacity to store over 2 million pairs of gloves. The warehouse is regularly pest controlled and fumigated to keep it pest and insect free.
The master cartons are sealed with colored tapes, with each color representing a particular size. This allows instant identification of size to our clients. The quality assurance passed gloves are container stuffed from the warehouse and shipped all over the world.
GMP FOR SURGICAL GLOVES
A glove is a protective device. A surgical glove is much more than a protective device – it is a medical device, used in invasive surgery in a sterile area. A good glove therefore should not have any bio irritants present on the glove, which can cause health hazards to user and patient. Natural rubber latex is the best polymer for surgical glove as it provides optimum barrier properties, elasticity, comfort, fit and cost and has been used for centuries.
However, recently latex gloves have come to be associated with latex allergies. What causes the allergy? Is it rubber latex or the manufacturing process adopted within the last two decades – first to meet increased demand and subsequently to reduce cost to sell gloves at a cheaper price due to competition, since supply currently exceeds demand? It is the unscrupulous manufacturing practices that contribute to latex allergies from gloves.
The critical parameters that need special controls, apart from the physical properties and dimension for surgical gloves are:
-
Leaching and quality of water used
-
Rubber chemical residue
-
Packaging material and packaging system
-
Sterilization process and sterility assurance
-
Barrier properties.
-
Bacterial endotoxin levels
-
Bio burden level on gloves
-
Toxicity
-
Quality and quantity of donning powder
-
Moisture content on the gloves
-
Extractable latex protein